Austin, Continued – From Downtown to Esperanza
I’m again enjoying having a real camera on my phone, so I wanted to further chronicle my adventure to one of the American capitals of YIMBYism. Downtown Austin has so much development, the American-Statesman has a whole page dedicated to new towers that are opening in 2024 alone. You can see it when you’re downtown, but you can also see it when you’re far away from downtown owing to the plethora of crane-age surrounding the skyline.
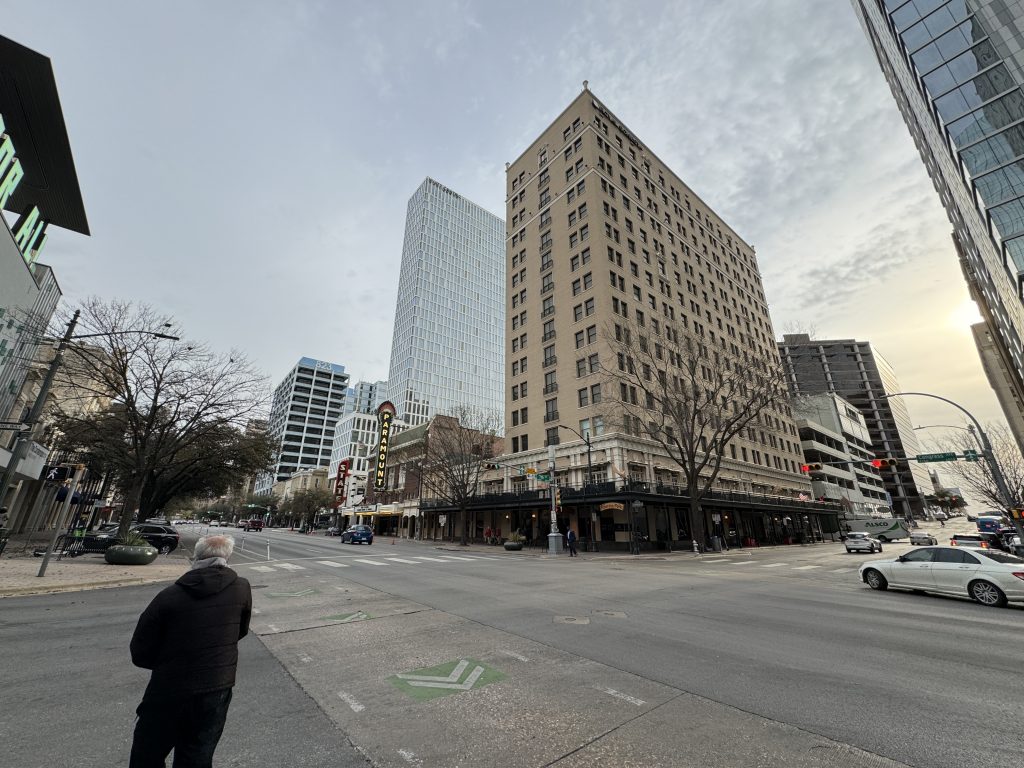
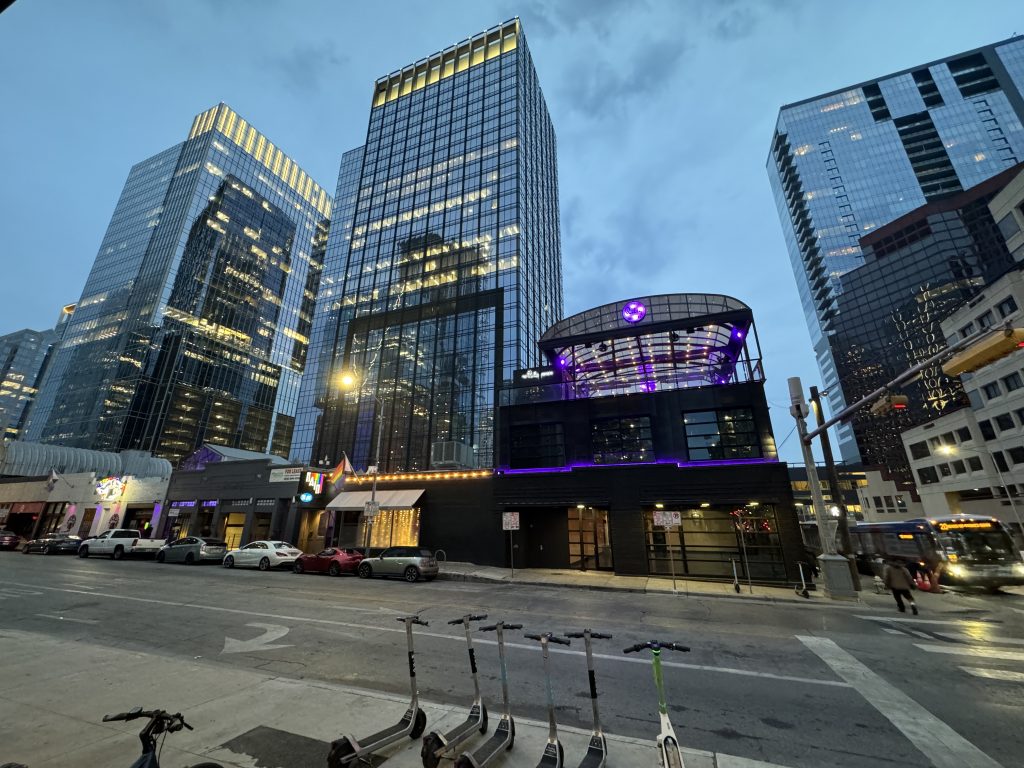
We’ve read a great deal about the crisis of homelessness in American cities. While the coastal cities of the Temperate West seem to dominate the popular discourse on this subject, homelessness is an issue in most American cities these days, and it has worsened directly proportional to the housing crunch as a limited housing supply combines with institutional investment in a scarce asset to form a disastrous twofer of unaffordability. Texas, however, has made headlines for the way some of its cities have dealt with it, and Austin shows us an interesting example as well in the form of the Esperanza community.
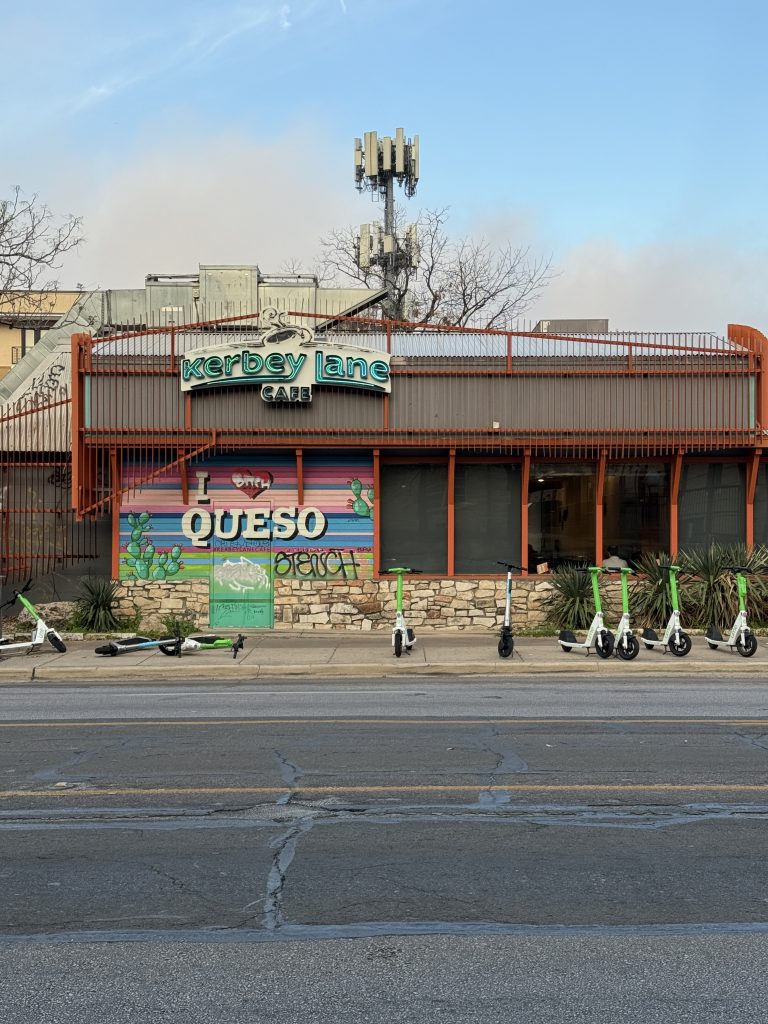
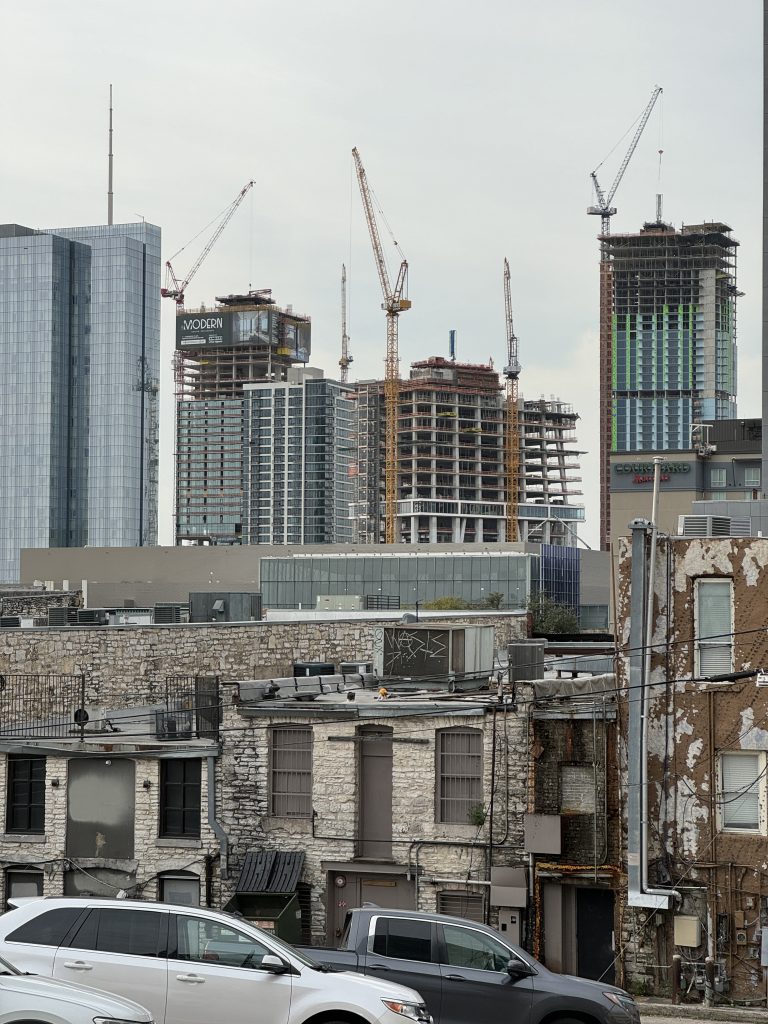
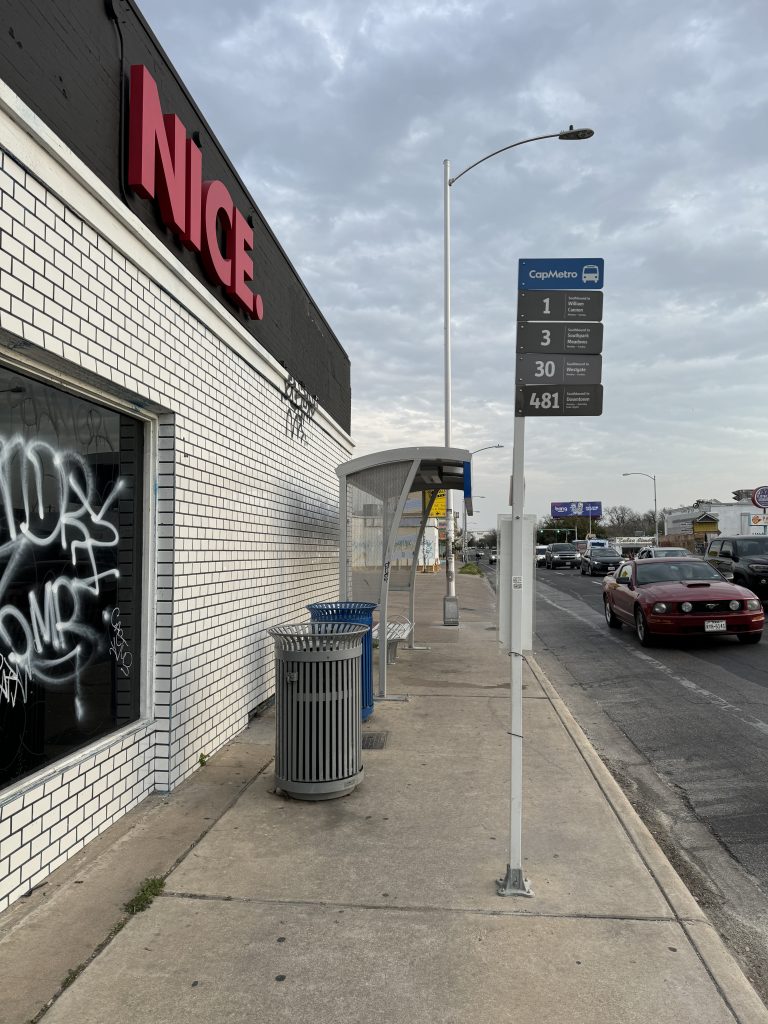
Esperanza is a “non-congregate emergency shelter” (emergency temporary housing in which people are living in separate rather than shared spaces) that was built on a former TxDOT site in the far eastern edges of Austin, what we planning nerds might call a “periurban” district. The site used to be used for TxDOT vehicle storage and maintenance, and a combination of entrepreneurial volunteers, construction experts, and community development professionals spent much of 2023 cleaning up and renovating the site.
Micro housing units, each with their own heating and cooling unit, serve as bedrooms, while communal facilities are provided for showers, bathrooms, and kitchens. The units themselves were actually built by none other than the founder of Tito’s Vodka, given that entrepreneurs with access to manufacturing and production resources can sometimes come up with wild ideas that they have the power to actually execute at scale, I guess? There is also a main building that features community space and offices.
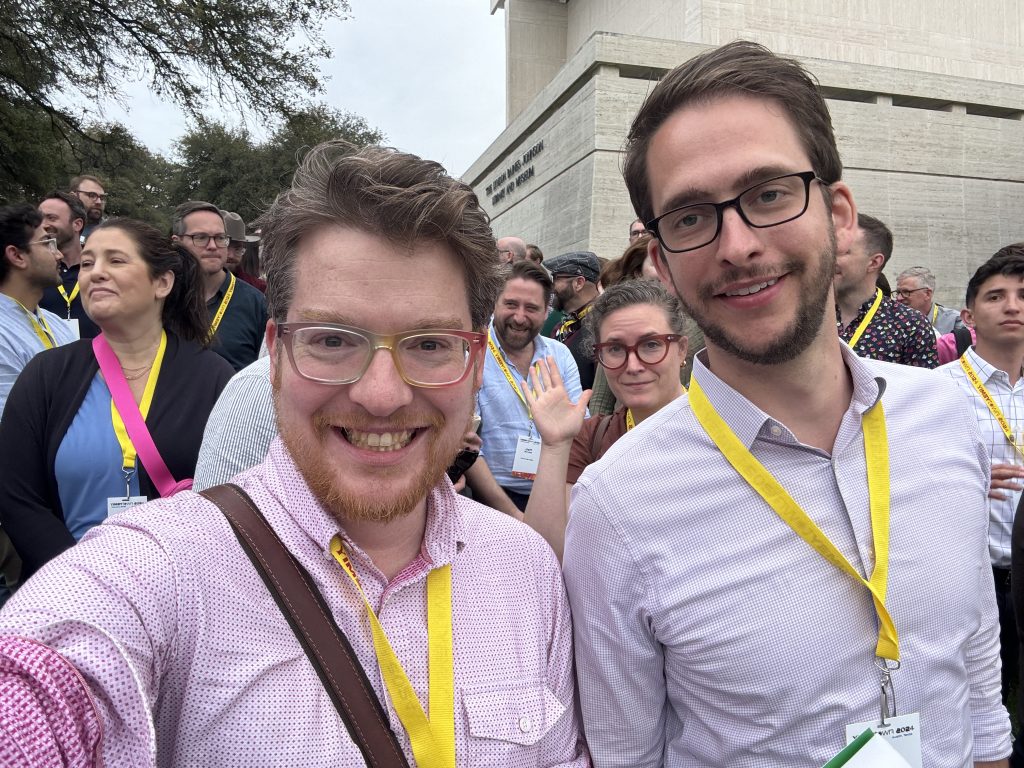
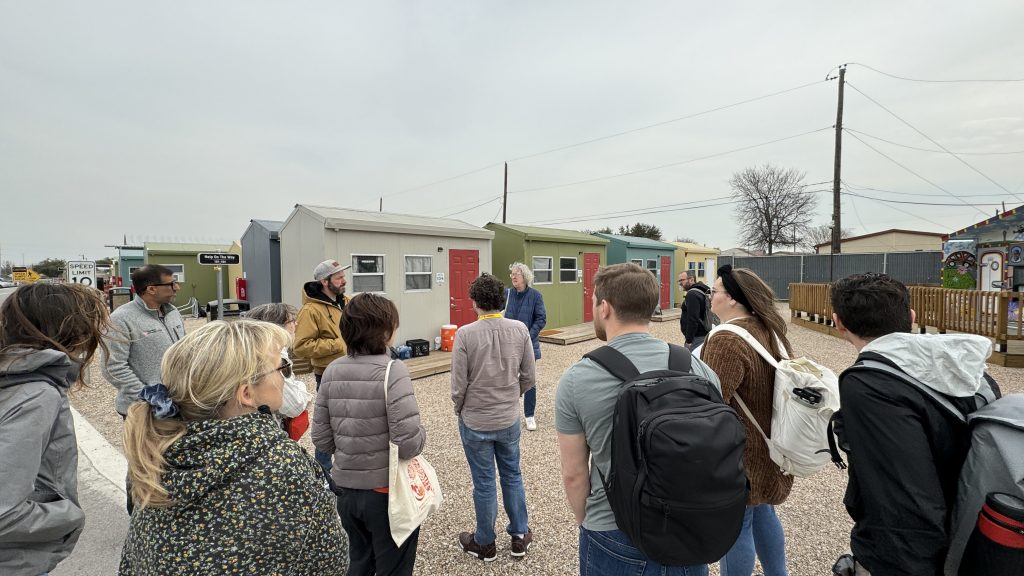
One of the more interesting things about Esperanza was the entrepreneurial spirit that seemed to surround the development process. There was a lot of, “we tried this, and that didn’t work, so we tried something else instead.” I think about this a lot in the context of discussing industrialized construction because there are so many unanswered questions, mostly around the regulatory process.
The way our host explained it, they had arrived at this site, where the state department of transportation and police had effectively dumped all of the homeless population downtown, and it essentially resembled some unholy rendition of Mad Max. They were essentially told by the owners and former operators of the site, “I don’t know, figure it out!” And thus a lively and diverse crew of practitioners sprang into action to try and figure out how to ensure that the unhoused population of the city could have access to resources, a clean, safe, and appropriately heated or cooled place to sleep, and, most importantly, a modicum of human dignity that every person deserves.
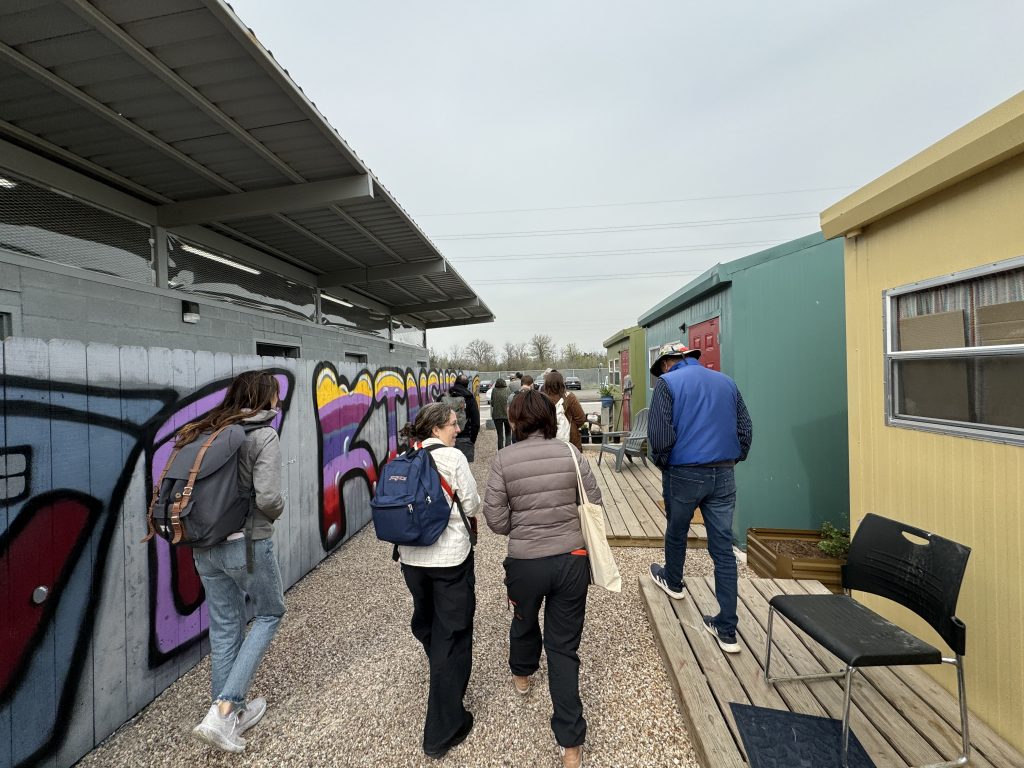
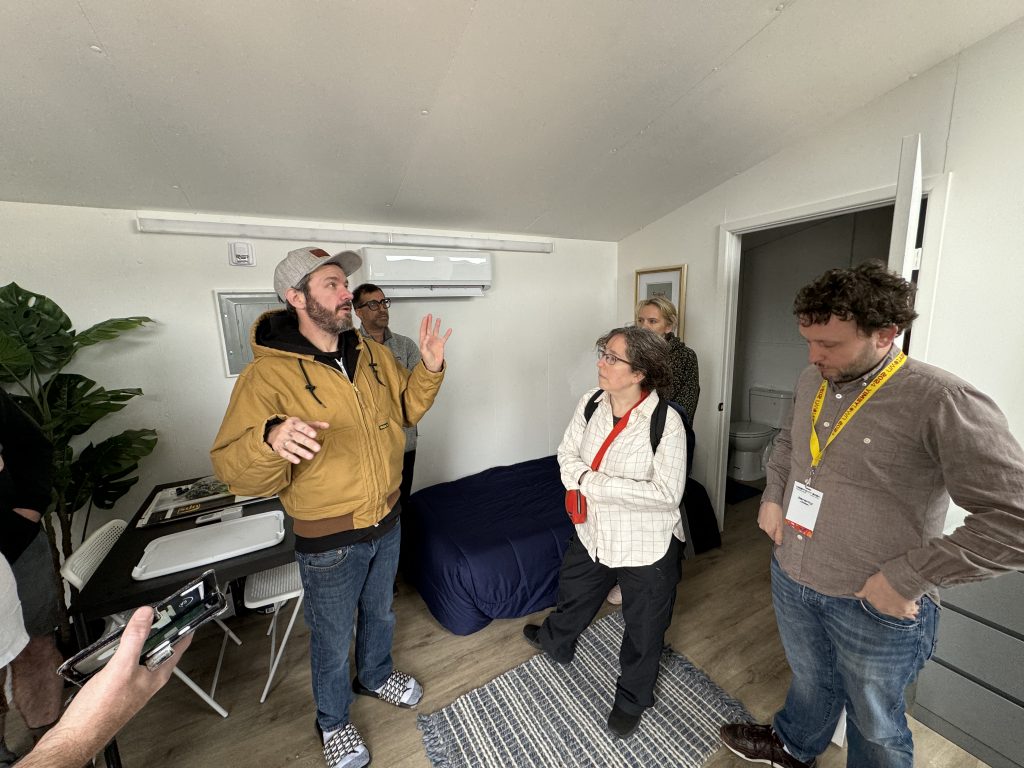
What was really interesting to me as I think about our current project with the ULI Larson Program in Detroit, which involves proposing some solutions attached to the Pope Francis Center’s new transitional housing and emergency shelter in Core City, was the way Esperanza seems to have been set up to allow some degree of experimentation around future developments. This doesn’t mean experimenting with the safety or accessibility of the site, which is one of the necessities of maintaining such a shelter. But rather, it comes in the form of exploring alternative avenues to new housing options, like a SIP-built house that we toured.
The host, who wore a Harvard Kennedy School knit jacket (bold thing to wear to a homeless shelter, to be honest), told us about the way they operated a factory in China that made the structural insulated panels, that were then shipped across the ocean to be assembled in Texas. It was a charming little house, all told, but built at a cost of upwards of $200 a foot. (For a point of comparison, $200/ft. for our industrialized construction products will get you a substantially nicer product that is American-made in the Southeastern United States).
“You shipped blocks of Styrofoam from China?” I asked, incredulous. “To build this thing?”
“Well, everything’s made in China,” he said, clearly bristling at my impertinence.
So it may well be!
But while I was skeptical of the China-to-Austin-periurban pipeline, I was at least glad that The Other Ones Foundation was open to the idea of creating new housing using new methodologies. That’s the value of partnership with open-minded people who know how to get stuff done. And that’s the kind of partnership I always want to look forward to forming with new collaborators. I’m still not sure I’m entirely sold on Austin as it involves a lot of extremes of various competing paradigms that I’m still trying to get my head around. But it was great to see this success story of innovative approaches to shelter and housing in an age that needs more of them.