Better Living With Robots: Scanning Buildings For Energy Efficiency
Last week, I had the opportunity to attend a webinar of the Advanced Building Construction Collaborative, a co-production of RMI and ADL Ventures, among other partners, that dealt with a topic I am all too familiar with: scanning buildings to inform better energy modeling and construction planning. Avideh Zakhor of Signetron and Kurt Roth of Fraunhofer USA presented on the use of precision LiDAR scanning technology to create high-quality BIM models and point clouds in the process of planning building envelope retrofits. Specifically, their products were custom-fabricated panelized exterior components designed to fit together and be applied to the exterior of an existing structure.
ABC is one of the venues through which we work on promoting (and exploring) concepts within the realm of industrialized construction (“IC”), a fancy coverall term for a variety of building technologies in which things happen off-site in a factory versus on the job site itself. The value propositions of IC are clear, but the implementation relies on finding people who want to use what they perceive as a new construction method. There are also regulatory challenges in that many municipal building departments don’t entirely know how to deal with IC products. In this case, we’re not talking about fabricating entire buildings, but rather exterior cladding that can be used to retrofit a structure to achieve higher energy performance.
Existing buildings are absolutely vital in the conversation around decarbonization, and especially in the conversation around equitable decarbonization (my, ahem, LinkedIn tagline), given that we can’t all afford to move out to the woods to build a brand new Passivhaus for $500/ft^2. Energy efficiency standards in the United States are barely as old as I am, and even then, an exterior wall that was R-10 at best without air sealing is compared to a virtually airtight wall assembly with an R-20 rating that is considered best practice today.
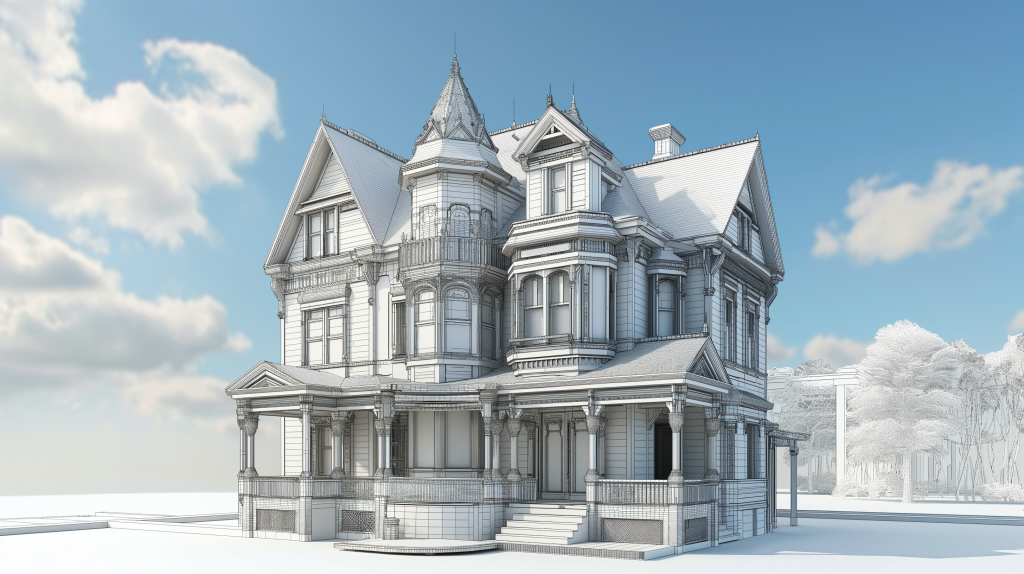
LiDAR, EIFS, PIR, and All Other Acronyms
Why, I asked, would you do these components and not a technology like EIFS? EIFS, if you’re unfamiliar, is an exterior insulation technique that essentially involves gluing styrofoam or another insulation material to the outside of a structure and then finishing it with a durable stucco-like material. The answer? Apart from the fact that EIFS often makes a truly tremendous mess in which lazy building trades often blanket an entire site with styrofoam particles (I’ve seen this more times than I care to admit), the value proposition of the Fraunhofer/Signetron models is that it can be done faster with less labor and more precision.
Zakhor did acknowledge the challenges of using BIM to achieve accurate modeling, because, she noted, BIM software is optimized for building new buildings, not wonky agéd structures in which absolutely nothing is square whatsoever. In our house, for example– a stately 1895 Victorian with a turret and fire damage that was repaired in a thoroughly half-assed manner decades before we bought in 2018- there are rooms that have a few inches of drop between the door frame and the middle of the room. This presents a challenge, as unless this wonkitude is incorporated into the geometry of the model (and therefore the component fabrication schedule), you might well end up with exterior insulation blocks that simply don’t fix together properly.
This was perhaps my biggest skepticism of the technology (to say nothing of cost, which a lot of scientists often just don’t even mention). But I see a lot of value in using LiDAR or technologies like Matterport to create thoroughly detailed, accurate scans of buildings for other purposes– like, among other things, creating highly detailed energy audits. Certainly, the historic district here would not approve vinyl-cladded polyiso blocks to be attached to the outside of our home. But it’s a fascinating, novel use of an established technology that could be vital in helping decarbonize a variety of existing structures.